|
Post by Bodaggit23 on Mar 5, 2010 2:01:21 GMT -5
I talked to our lead engineer today, the one that's taught me most of what I know about modeling, and he fixed the neck pocket for me in about 60 seconds. He even complimented me on my model! Woot! Anyway, he showed me a different way to sketch the cuts also, reducing the amount of features in the model, and in turn it smoothed everything out immensely. Here's a side by side comparison, the RIGHT picture is before: 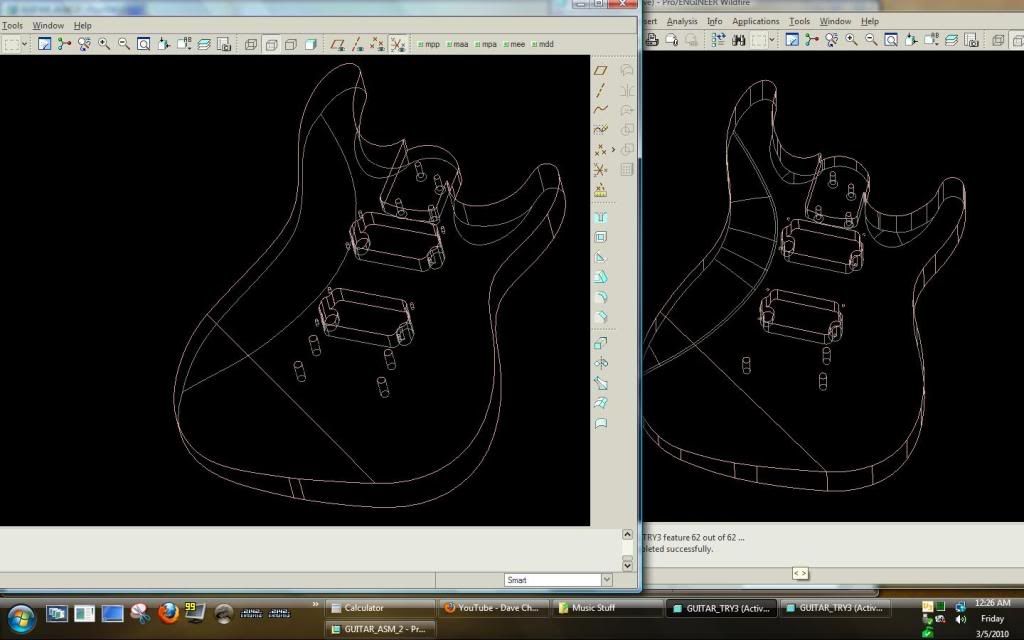
|
|
|
Post by heem6 on Mar 5, 2010 12:36:04 GMT -5
Nice job figuring out that neck pocket! I know you had help, but you still knew what the problem was and what was needed to fix it.
Are you going to paint it yellow, like the first mock ups?
|
|
|
Post by Bodaggit23 on Mar 5, 2010 14:34:59 GMT -5
No sir.
It will be polished to a mirror chrome finish.
|
|
|
Post by heem6 on Mar 5, 2010 21:11:58 GMT -5
As Paris Hilton would say....
Wait! Fukk that! I'm not quoting HER!
Anyway, Mirror Chrome finish sounds HOT.
It's really interesting to watch your progress thru your posts in this thread.
|
|
|
Post by Bodaggit23 on Mar 6, 2010 2:34:55 GMT -5
Thanks for watching! ;D I'm glad I'm finally following through with this because it's something that I'll always have, and be proud to say I made myself. The guitar will be done in two weeks...another day like today and I'll be finished modeling and be ready to order material and create the programs. I'm having a blast, but it's becoming tedious. I don't know how our engineers can do this day after day, for years. I spent many, many hours today after work hollowing out the bottom "half". The way it works out is the bottom will be 1" thick and the top will be 1/2". Here's a few pics of the bottom, almost 100" done, with a bit of color added to show depth. EDIT: You'll notice the funny surface in the neck pocket. This is because the pocket is "shimmed" or "ramped" as explained previously, and creating a flat surface around the outside of the pocket will allow me to get a Ball Nosed End Mill running back and forth, to create the angled surface. It's an easy fix.  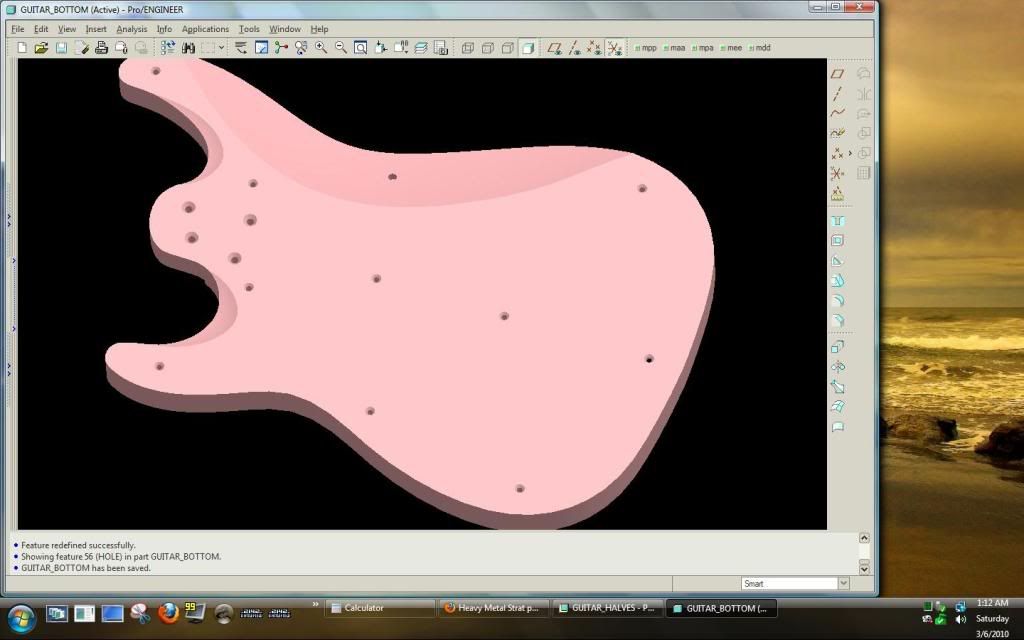 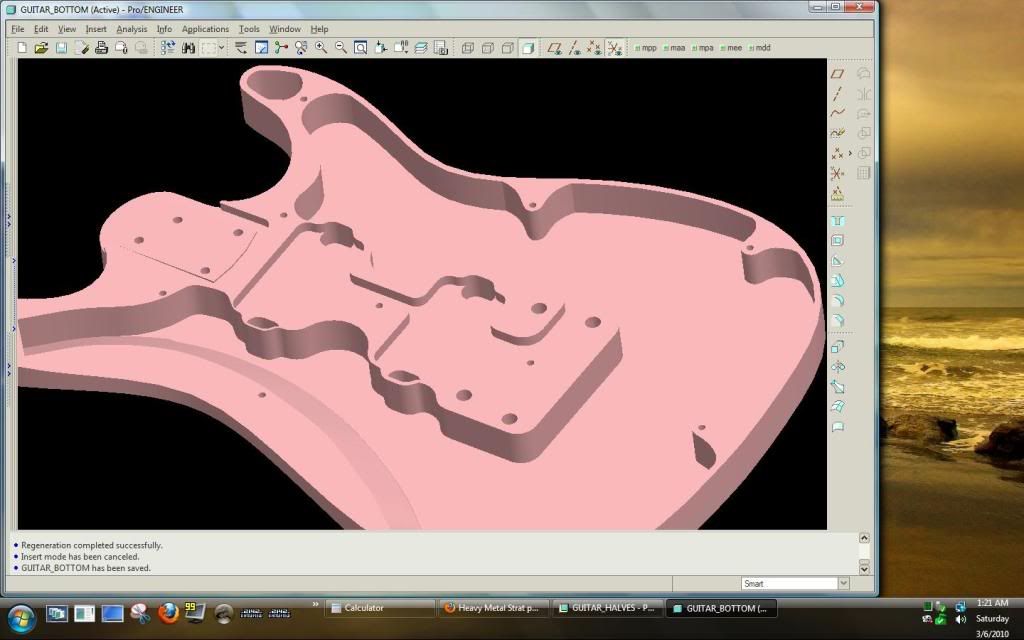 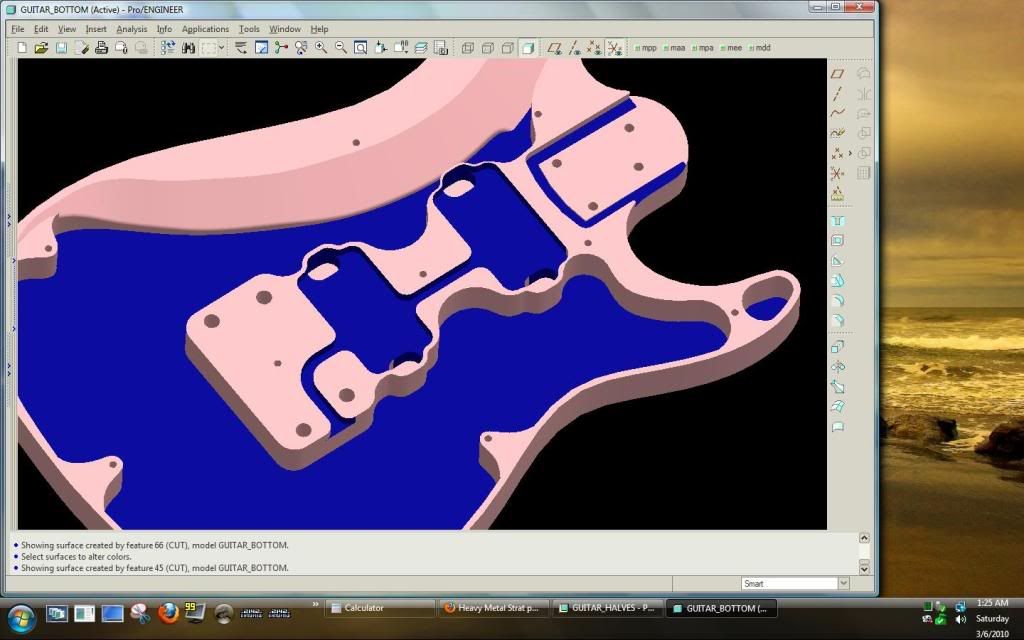
|
|
|
Post by Bodaggit23 on Mar 7, 2010 3:37:17 GMT -5
Ok, slight change of plan. The material I was going to use is way too expensive for me right now, so I've decided to create the body in "Modules". I know it won't be as solid, and it will be a bit heavier, but this way will cost me 75% less! I could add a solid top later if I want, and maybe eventually a solid bottom. Every piece is aligned with dowel pins, so it should blend fairly well, but it won't be perfect. Oh well. I'm going to start making these 6 parts tomorrow! 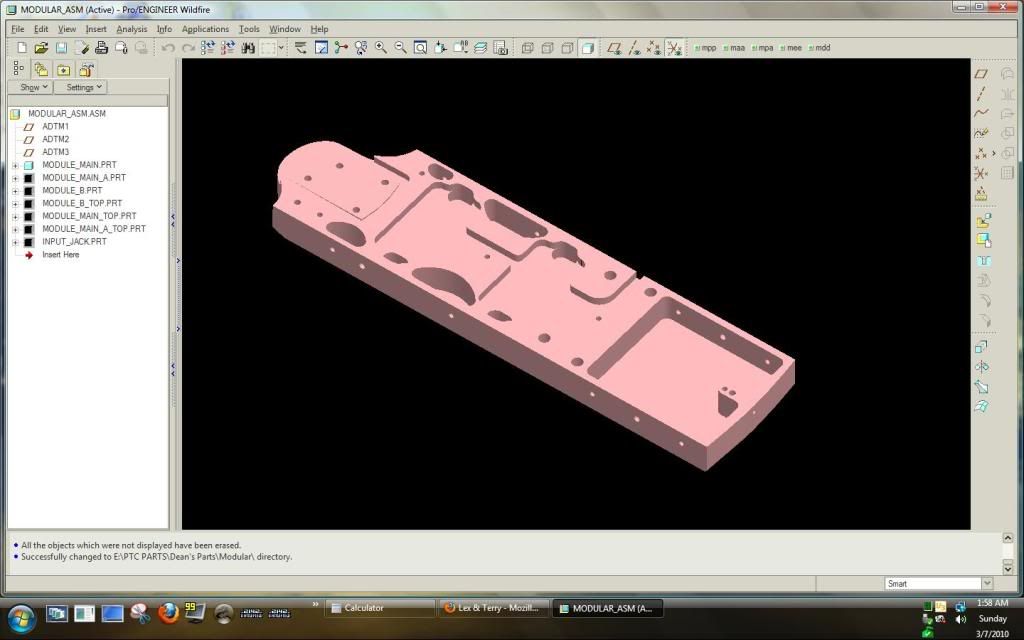 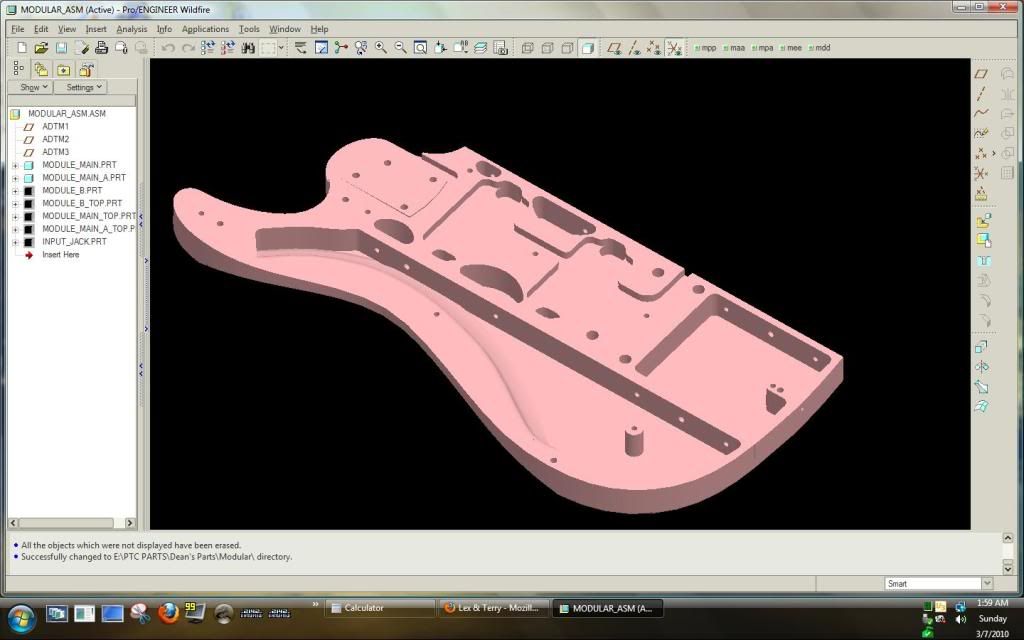 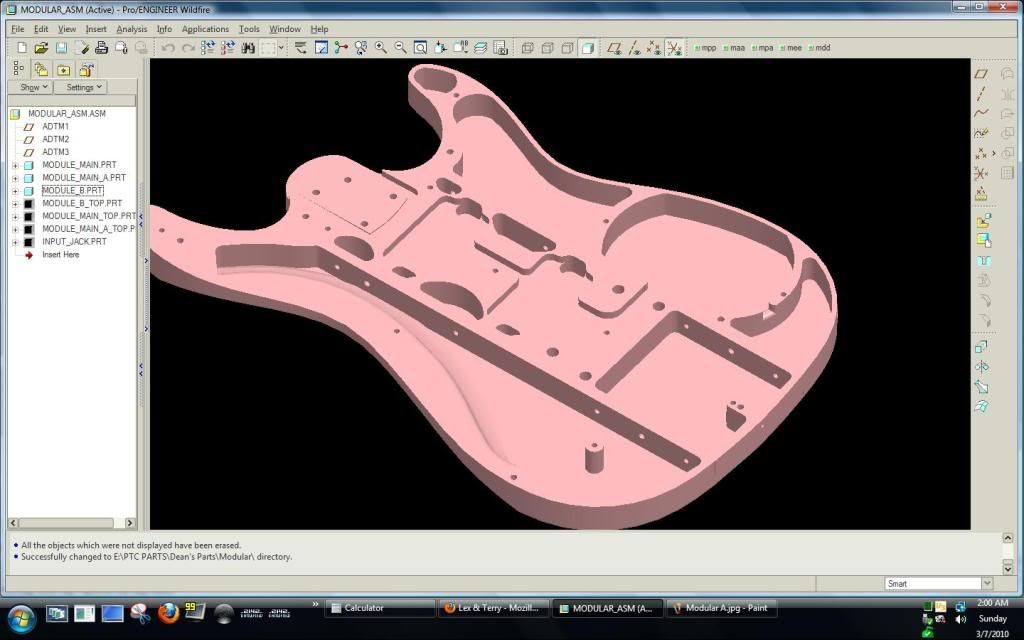 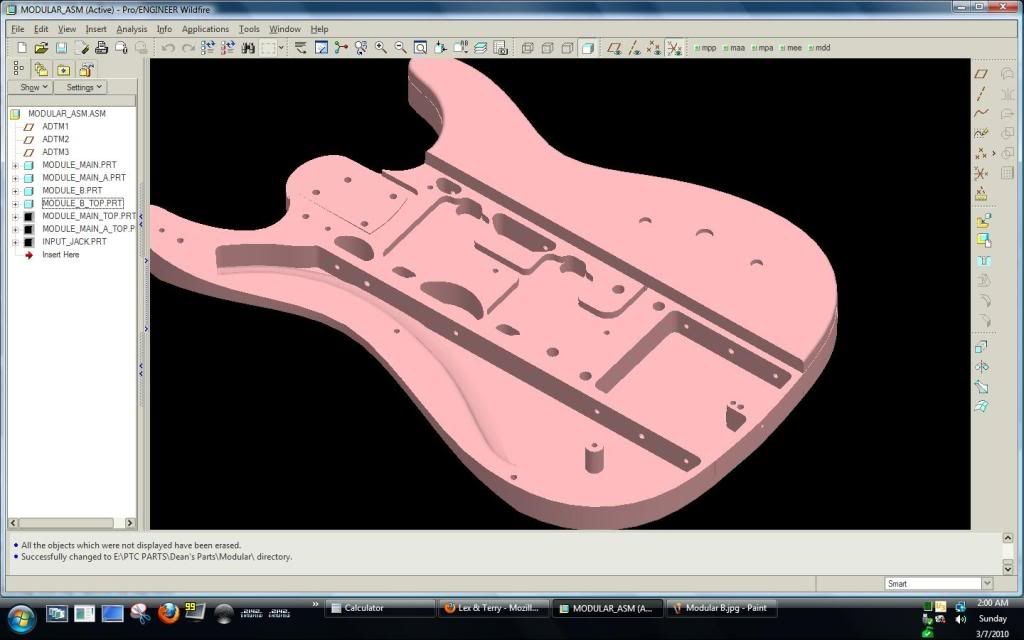 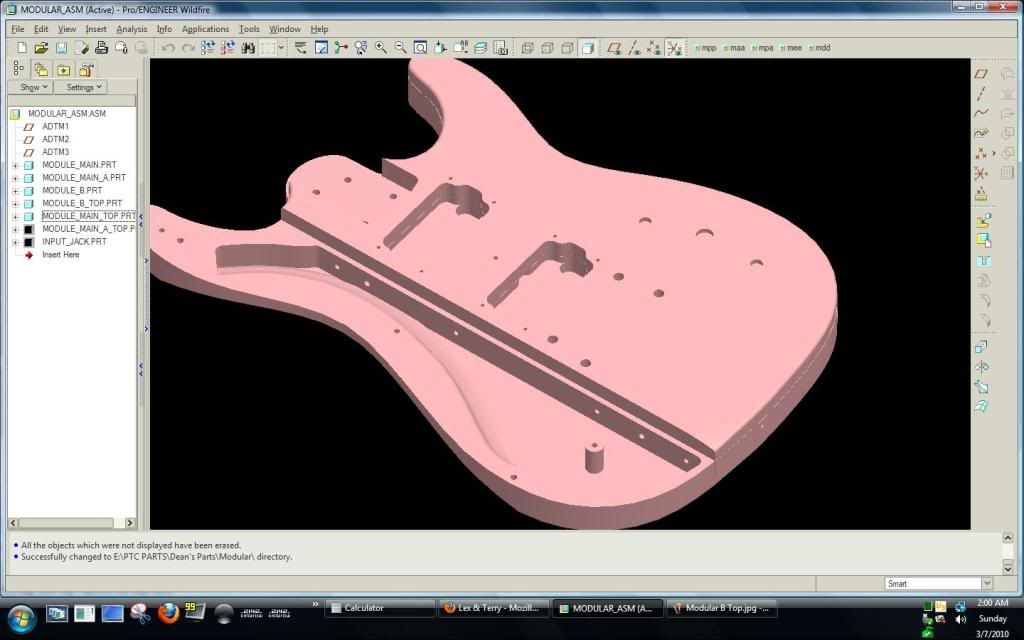 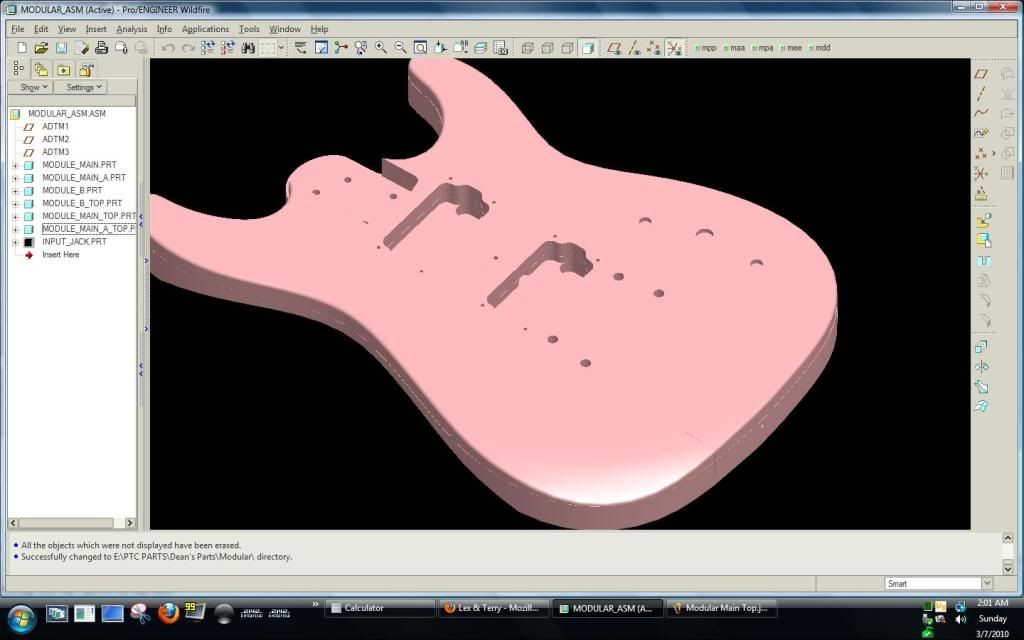
|
|
|
Post by lbeast on Mar 7, 2010 12:19:29 GMT -5
If I sent you a solid piece of Lucite do you think you could make a Lucite HM body?
|
|
|
Post by Bodaggit23 on Mar 8, 2010 1:12:24 GMT -5
If I sent you a solid piece of Lucite do you think you could make a Lucite HM body? Most definitely. That material would present it's own unique issues though. The only way I could hold it down to cut around it, would be to put tapped holes in the back. And you'd have to figure out how to drill the hole between the pickups for the wire! ;D
|
|
|
Post by Bodaggit23 on Mar 8, 2010 1:16:44 GMT -5
|
|
|
Post by heem6 on Mar 8, 2010 11:33:56 GMT -5
That's really nice work, Bo! And spot on with the 25.5" scale length. What do you use to polish aluminum? P.S. That guitar is really 
|
|
|
Post by Bodaggit23 on Mar 8, 2010 11:37:13 GMT -5
Indeed. She's gonna be a heavy weight for sure.
Definitely more of a conversation piece than a daily player.
Polishing, we have a huge two sided bench grinder with a scuffing wheel and a polishing wheel. Along with sticks of polishing compound, varying in degree of grit.
You basically scuff it all up until it's all even, then rub the polishing compound on the polishing wheel and buff it until it's shiny, like chrome.
|
|
|
Post by heem6 on Mar 8, 2010 15:16:45 GMT -5
How much do you estimate it will weigh, after all the hollowing you've done?
|
|
|
Post by Bodaggit23 on Mar 8, 2010 16:28:24 GMT -5
Well, I just weighed the first piece and it weighs 3.8 pounds. Not sure exactly. Let me get back to you. I'll ask an engineer if Pro/E can tell me how much each piece weighs. I'll guess....20 pounds finished? Quite a leap over an 8 pound HM. 
|
|
|
Post by Bodaggit23 on Mar 8, 2010 16:40:46 GMT -5
Ok, I asked how to figure Mass in Pro/E and I came up with the following weights for each part:
Main Bottom: 3.78 Bottom B: 1.35 Bottom A: 2.13
Main Top: 1.44 Top B: 9.8 Top A: 1.34
There's obviously an issue with "Top B" as I know it won't be almost 10 pounds. I'll guess 1.5 for that part.
So, for a total of all parts, no hardware, 11.54 pounds.
We'll see.
|
|
|
Post by Bodaggit23 on Mar 8, 2010 23:28:23 GMT -5
No update today, sadly.
No machines available tonight.
We have a bunch of parts that need to go to anodizing tonight.
Tomorrow hopefully.
|
|